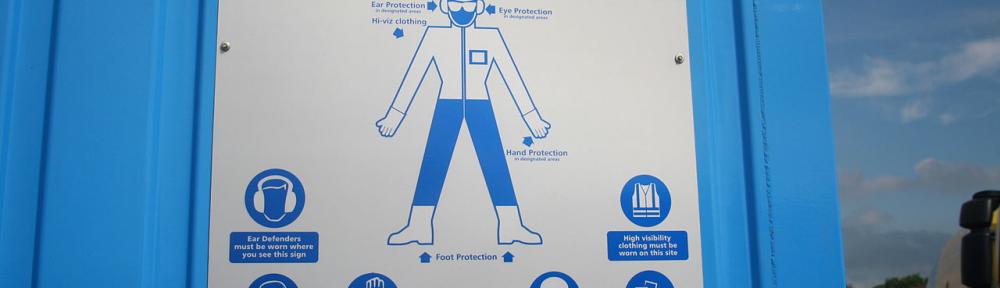
Using your Head – A Guide to Head Protection
Posted on October 20, 2017
With a huge variety of different head protection available, how do employers make the right choice? In the second of a three-part series, Keith Hole, vice-chair of IOSH’s Construction Group and Head of SHEQ at MTS Cleansing, looks at the options.
There is a huge amount of choice when it comes to deciding which form of head protection employees and visitors should use.
Many people immediately think of hard hats when they think about head protection. There are, however, many more options.
When choosing, you should ask yourself a series of questions. What hazards is the individual exposed to? What other mitigations have been put in place? Who is the head protection for (someone working on site or a visitor, for example)? What weather conditions will the individual be working in?
Don’t forget that you should check the head protection you provide to visitors each time you issue it to ensure it is fit for purpose.
Once you have answered those questions, you can go on to looking at the different options and decide which is right in your workplace. The following are a few examples of the options and why they might be chosen.
Head Protection
Industrial bump caps
These are suitable when the risk posed is as the name suggests; bumping or walking into objects. An example is in warehouses or garages, where you may have an individual working underneath a car. Their main purpose is to prevent bumps and grazes. They are not intended to provide protection against falling or moving objects.
Bump caps are not tested for lateral deformation and will not protect from severe impact or crushing injuries. If you were wearing a bump cap when you sustained a severe blow to the head, it wouldn’t prevent a skull fracture.
Bump caps often come in baseball cap style, which can make them more comfortable and more likely to be worn in low-risk environments and tend to be very popular with delivery drivers and warehouse staff.
Industrial safety helmets
These are suitable for a wide range of working environments because of the range of hazards they protect against. You can consider options such as vented safety helmets to make them more comfortable in hot environments and liners can make them warmer in cold weather.
Unvented helmets are better for use in areas where you require protection from chemicals and liquids with many unvented helmets protecting against molten metal and electric shocks of 440V ac.
There are various other design features which can be selected to ensure that the safety helmet is fit for purpose, for example peaks or no peaks, increased impact protection and the addition of accessories for hearing protection.
While many accessories can be added to head protection you should also consider the compatibility with other forms of PPE such as Respiratory Protective equipment (RPE), eye protection, face shields and hearing protection.
Industrial climbing helmets
These have a suspension system and shell structure that has been designed to be used for industrial, mountaineering, rescue and leisure activities.
Tested to mountaineering standards in addition to industrial standards, they provide protection to those undertaking rope access work or other activities where a greater range of hazards may be present. Still allowing the connection of accessories that may be required in an industrial setting as above.
Keeping it on your head
The fact that a hard hat sometimes comes off, particularly on receiving an impact, can defeat the purpose of wearing one.
One way of combating this is the use of chin straps. All hard hats should have fixings to attach a chin strap if needed. It is well documented that the use of chin straps is an effective tool in reducing head injuries.
The challenge with them is that they can be uncomfortable and may make users likely to just undo them, thus removing the protection that the chinstrap would provide – or worse still, remove the helmet all together.
Industrial climbing helmets will always have a four-point chin strap due to the hazards present in these working environments. Climbers tend to be more aware of the risks associated with their activities, so are more likely to comply with wearing a chin strap.
In contrast, there is a long-standing issue with people not wearing the chin strap on industrial safety helmets. In recent years, manufacturers have moved away from the combination of an adjustable ratchet band and chin strap combination. This has been replaced with a more user-friendly ratchet wheel.
The ratchet wheel enables the hat band to be tightened after the helmet has been placed on the user’s head and locks the hard hat in place. This removes the need for a chin strap in all scenarios, apart from those with a high probability of a significant impact occurring.
The ratchet wheel also removes the additional hazards of chin straps causing strangulation if the hard hat becomes caught or releasing early when a given force is applied. Thus leaving the user vulnerable to further impacts where these are received in quick succession.
Click here to see the most Dangerous Jobs in UK!
Source: IOSH